リサイクルを阻む4つの「壁」
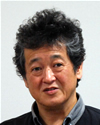
資源のリサイクルについても、時代とともにかなりフェーズが変わってきました。今までは「資源に何らかの価値があるから使おう」ということでしたが、現在は、既利用資源量が地下資源量を上回る状態になっています。すでに地下資源を探すのが困難になっている状況の中で、今まで使っていた資源はどこにあるのかというと、消費者、消費地にあるわけです。要するに、「資源の偏在」と「消費の偏在」が一致しているということ。日本に資源があるということです。
この資源をうまく使っていくことが重要になりますが、リサイクルを難しくしている4つの「壁」(「分散の壁」「廃棄物の壁」「コストの壁」「時代の壁」)があります。
「分散の壁」というのは、製品の1つ1つには少量の資源しかありません。しかもそれらは、消費者の手元に分散しているということです。前にも言いましたが、これは逆に1㎏の資源を集めるのに、どれだけの製品を集めなければならないのか、ということになります。
「廃棄物の壁」は、製品の中の必要な資源よりも、廃棄物の量の方が多いという問題です。例えば、金は鉱石の中に4ppmしか入っていませんが、携帯電話には0.5%入っています。金属はこれだけなのに、ほかはすべて廃棄物なのです。
「コストの壁」については、リサイクルをやっている人でもよく分からないでいます。実は、リサイクルの方法には2通りあって、1つは、廃棄物にスクラップと高品位材料を混ぜて希釈することで素材として再生させる“希釈型”のリサイクルです。鉄やアルミ、プラスチック、ガラス、紙などで使用されている方法です。もう1つは、廃棄物などから必要なものを高純度に抽出し、高品位再生材料として再生させる“抽出型”のリサイクルです。レアメタルや貴金属などで使用されます。
みなさんはリサイクルというと、抽出型しか頭に思い浮かべませんが、実際にやっているのは希釈型がほとんどです。抽出型で取り出す金属はわずかな量であり、残りの廃棄物の処理コストもかかります。ましてや抽出するのはレアメタル類ですから、金額は低いのです。1台の携帯電話にある金属は100円程度ですから、生半可なところでは経済的には成り立ちません。ましてや抽出コストも最適化されていないので、さらにいろいろと経費がかかることになります。
「時代の壁」というのは、まだモノづくりがリサイクルを組み込む段階に至っていないという時代的限界です。これまでの手間やコストのかかった後付け方式の20世紀型リサイクルを改めて、製品から容易に資源を分離できるような易解体設計や、高品位品位の再生金属を高付加価値生産に利用できるようなシステムが求められているということです。
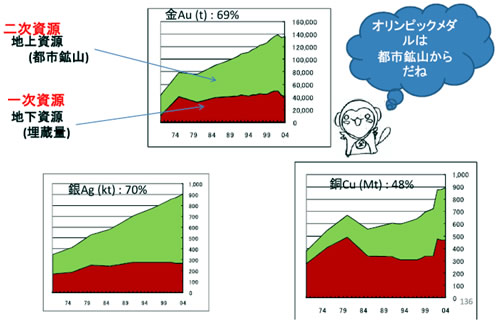
日本で根付かないリサイクル産業
もう1つ言っておきますと、リサイクルには「資源の再利用」という“goods”の側面と、「廃棄物の処理を減らそう」という“bads”の側面があります。前者が経済産業省、後者が環境省の視点です。今の日本のリサイクル法は環境省側の視点でつくられているので、廃棄物は悪いものだから、ため込んでおくことができません。
製品に含まれるレアメタルは少量だから「ためておけばいい」とも言われますが、ためておくと環境行政の法律体系に入ってしまうので、早く処分するしかありません。そういう問題もあって、リサイクルがなかなか難しくなっているのです。そうした状況だけに、今やっているリサイクルも単に、レアメタルを切って溶かしているだけです。日本にあるリサイクル会社約400社のうち、抽出までをやっているのは11社ぐらいです。むしろ、海外に流れているほうが多い状態であり、日本国内では産業としては根づいていないのです。
リサイクル問題の本質
産業として根づかないリサイクル、これが日本のリサイクル問題の本質です。要するに「リサイクルを一番欲しがっているのはだれか」ということです。
現在のリサイクルの構造は、世界中から資源を集めて、ハイテク製造業がハイテク製品にして、それを自治体が一生懸命回収する。さらにそれをリサイクル屋が解体して取り出し、金属に戻して、最終的に金属のインゴットにしています。そういう循環があるわけですが、一番金属資源を欲しがっているのはハイテク製造業です。本当はそうしたハイテク製造業が必要とするリサイクルを組まなければいけないのですが、今のところ、それができていないわけです。むしろ、資源が製造メーカーから出て、再び戻ってくるようなリサイクル、しかも資源が汎用製品としてではなく、高品位の素材として回ってくるようなリサイクルが必要なのです。
例えばコバルトの場合は、リチウムイオン電池からリサイクルして、インゴットにしています。コバルトをインゴットにして、超硬工具の製造に使うわけです。値段的にも安いわけですね。ところが、我々はリチウムイオン電池にするコバルトを欲しがっているわけで、そちらに回すリサイクルをつくらなければいけない。ところが今、どこが主にリサイクルをしているかというと金属屋さんなのです。それが大きな間違いであって、リチウムを高純度抽出し、化学リサイクル製品として回していくような新しいプロセスが必要です。あるいは必ずしも循環しないまでも、一時的な“サプライリスク”を支えるために、自分たちの市場からリチウムを回していけるような技術を持つことが必要ではないかと思うのです。
レアアースのリサイクル
金属資源のうちでもベースメタルやレアメタルに比べて、とくにレアアース(希土類)磁石のリサイクルは大変難しいのです。何しろ、磁石にするときに酸素がちょっと入っただけでもだめになるほどです。では、どのようにリサイクルするのか。ディスプロシウムやネオジウムなどを、それぞれインゴットにしてもほとんど意味がありません。新しい抽出技術だけではなく、酸素濃度の高い粉末スクラップ原料からでも利用できる焼結技術の開発、さらにリサイクルの処理中に特性を劣化させないような組成設計技術、磁石のリユースを目指した易解体技術などの開発をうまく進めていけるように、技術体系を全部整理し直すことも必要ではないでしょうか。
「消費者にものを与えない」
資源のリサイクルにも究極の答えがあります。「消費者にものを与えない」ということです。どういうことかと言うと、基本的には製品はメーカーから消費者に回しているわけですが、最終的には消費者にものを与えず、サービスだけを提供するというシステムです。
成功した有名な例が「レンズ付きフィルム」いわゆる「使い捨てカメラ」です。これは、消費者自身はフィルムを使い切ってカメラごと現像プリント屋さんに預けます。カメラのほうは分解されて回収されているわけです。資源のリサイクルとして考えた場合、実は、その後の商品にも物すごいチャンスがあったので。それは何かというと携帯電話です。携帯電話はそれに近いような形で一時期売られていましたよね。でも最近は、それも結局やめてしまいました。
太陽電池をやっている人たちにも、私が「次は太陽電池だよ。システムとしてきちんと売って、メンテも全部含めてやるべきだ」と話したら、「そんなことを言ったら中国に勝てませんよ」と言われてしまいました。ところが昨年、一番売り上げた太陽電池企業は「ファーストソーラー」でした。ファーストソーラーが太陽電池に使っているのはテルル化カドミウムです。太陽電池を設置して、使用中から最後のリサイクルまで全部面倒を見ているのです。まさにサービス・アイテムのやり方ですね。「あなた方は電力を使ってくださればいいのです」ということなのです。そうしたやり方が、中国の企業を抜いてトップを行っているわけです。
おそらく、最終的にはそういうシステムができていく。そうした資源のリサイクルシステムをつくった企業が勝ち抜いていくのではないかと思います。
世界に示す「WAの技術」
東日本大震災や福島原発事故、さらにエネルギー問題によって、日本はいろいろな制約を受けることになりました。資源あるいは工業素材の問題では、中国を主な相手とする「世界の工場」をめぐって争い、これまでは「安くてそこそこのものを早くほしい」という世界の需要にどう応えるかが日本の課題でした。しかし大震災が起きて、日本からの素材供給が停止するなど、リスク管理上の問題から、世界の需要も「ここだけのもの」から「どこでも手に入るもの」へと変化しました。これは日本の企業にとっても、重要なポイントになります。
「世界の工場」をめぐる争いについては、もはや「つき合う必要はないよ」というのが私の結論です。世界の8割の人たちの需要にこたえて「安く、早く」売りつけようとしている中国の「工場」が、おそらく今後10年間は支配的になると思います。しかし、そうしたときにクオリティ問題など、いろいろな問題が出てきます。そうしたときに「安心できるシステム」や「サステナブルなシステム」などが必要とされる時代が、必ずやって来ると思います。そういうものを準備する「ものづくり」を、日本が今からやっていく必要があるのです。
今のこういう時期でも、すでにマイクロガスタービンによる分散型の発電技術や、六本木ヒルズ一帯でのコジェネレーション・システム、LEDを活用した照明設備などがすでに実現しています。さらにレアアースを活用して、モーターとインバーターとを組み合わせた「スマート・システム」にサステナビリティを持たせるような製品を作り、中国が「安くて、そこそこのもの」を世界にばらまいた後に、世界に販売していくような方向性をもって、今からそうした技術を準備しておくことが重要ではないでしょうか。
世界的な物流チェーンの転換が始まろうとしている中で、今の日本が持っているようなサービスやシステムを組み込んだ新しい技術システムや、その流れをつくっていくことも必要です。これはある意味では「顔が見える技術」を見つけるチャンスかもしれません。「どういう材料をどういうふうに使い込んでいったか」をきちんと見ていくような、一連のサービスと材料技術とが一体化したものをつくっていくのです。そうなれば「日本の製品、システムが欲しいから日本に資源を回せ」となるかもしれません。そこまでしないと、資源問題には対応できなくなるのではないかという気がします。
そこで、私が強調するのは「国際的な視点」です。日本が「ものづくりジャパン」を意識して力を合わせながら、新しい「世界の工場」の流れの中に日本型の生産システム、物質利用システムをつくっていくこと。そのために、みんなが知恵を出し合う必要があるのではないか。
私が考えたのは「和のサービス」であり、日本が世界に示す「WAの技術」です。「WA」という文字にはサプライチェーンの「輪」、調和の「和」、循環の「輪」、日本国内の「和」もかけています。そうした方向性を日本全体で共有しながら、日本には「素材技術があるよ」「ものづくりの技術もあるよ」といった大きな絵を描くことが今必要なのではないかと、思っています。
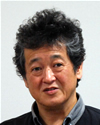
(はらだ こうめい)
原田幸明(はらだ こうめい) 氏のプロフィール
長崎県壱岐生まれ。1969年壱岐高校卒業。74年東京大学工学部卒、79年同大学院博士課程(金属工学)修了(工学博士)。80年科学技術庁金属材料技術研究所研究員。2001年物質・材料研究機構エコマテリアル研究センター長。2005材料ラボ長。2011年から現職。