折り紙は海外でも「Origami」として認識される日本の誇れる伝統文化だ。その代名詞である「折り鶴」を手慣れた人が単純に折るのに時間はかからない。しかし、例えばウサギを精密に折るとなると10時間はかかる。そんな手間を省き、山折りと谷折りのパターンを作成し印刷したシートにお湯をかけると、最大10万本以上の折り目と数万個の面を数秒から数分の内に自動で折って立体形状となる折紙シートの技術が開発された。アパレル、医療、宇宙産業など幅広い分野での利用が期待できるという。

3Dプリンターの課題 折り紙の「自己折り」で解決
3次元形状の製造は3Dプリンターの発展で手軽になりつつあるが、プリンターの大きさにつくるものの大きさが制約される、完成まで自重で壊れないように構造を維持する「サポート材」が廃材となる、完成したものが複数になると場所をとって保管や運搬が難しくなることが課題となっている。東京大学大学院工学系研究科の鳴海紘也特任講師(デザイン工学)らは、紙のように2次元で保存できて必要なときに素材自体が変形する「自己折り」が起こる折紙シートの開発で、これらの課題が解決できると考えた。
鳴海特任講師らは、将来の汎用性を高めるために、工場や工房などで使用される市販のUVプリンターを使うことを決定。家庭用インクジェットプリンターと同じようにインクを飛ばして模様を描く印刷機だが、紫外線で乾くインクを使うため、通常のインクより乾きが早く、折紙シートを短時間につくることができる。
印刷する素材には手に入りやすい熱収縮シート(ポリオレフィンの透明なフィルムやポリエステルの布)を採用した。谷折りと山折りのパターンを印刷し、熱を加えることでシートが収縮し、自動的に折り紙が完成する仕組みだ。
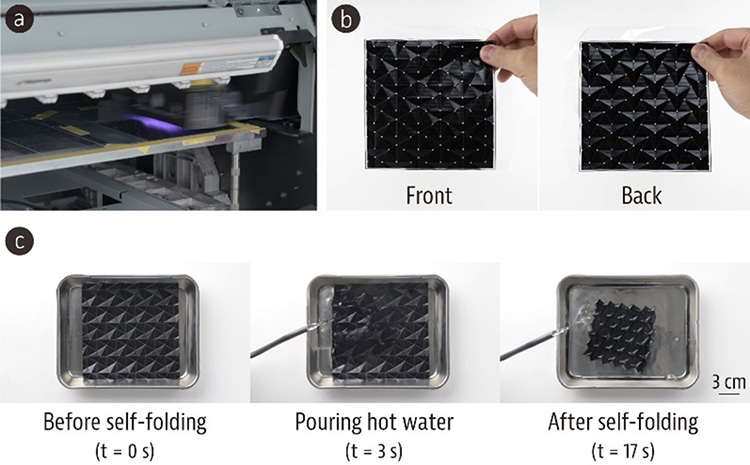
折り紙の谷折りと山折りは、熱収縮シートの表と裏どちらにインクを塗るかで決める。インクがある部分がシートの収縮を妨げ、インクが塗られていない方向に折れる仕組みになっている。インクの層の硬さが変わらない程度の70度~100度の加熱では、熱収縮シートが5%ほど収縮することから、完全に180度折り曲げたいときには1ミリほど折り部分に隙間を持たせた。今回の研究では、黒インクを5層塗るなどしており、完成する折紙シートは、紙3枚分程度(0.3ミリ弱)の厚さになっている。
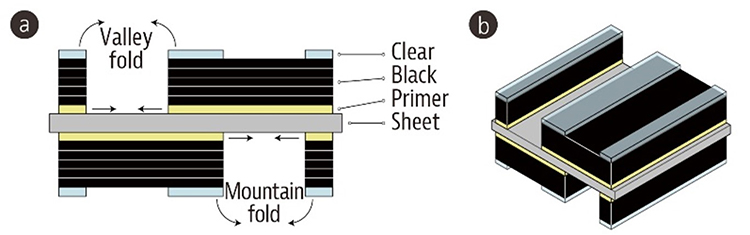
1辺3ミリ 従来の1200倍の解像度を実現
これまでの研究では、折紙構造を自動で折ることができる折り線や面の数は最大で100程度だった。今回開発した折紙シートは、600×600dpi(dpiは1インチに並んだドットの数)の解像度を設定してパターンを印刷していることから、1辺3ミリという細かさの線を折ることができる。その結果、これまでの研究よりも1200倍の解像度になり、最大で10万本以上の折り目と数万個の面を持つ折り紙を、湯をかけるだけで数秒から数分の内に完成させることが可能になった。
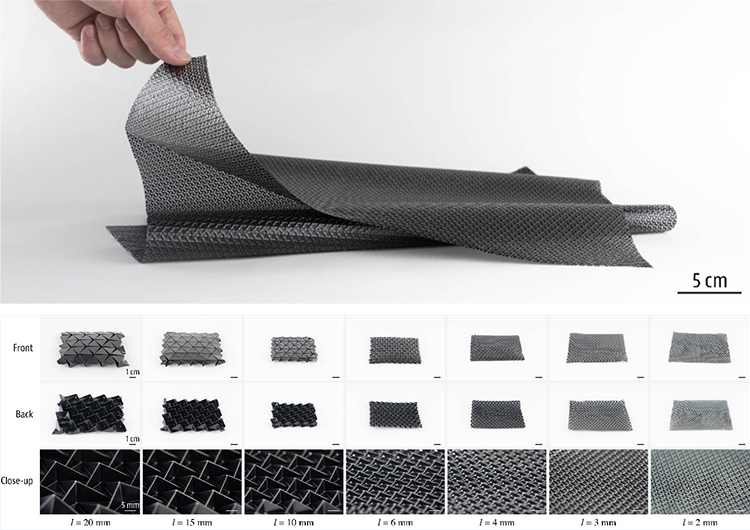
研究グループでこれまでに開発した折紙設計ソフトウェアのOrigamizerとCraneの機能を拡張したことで、設計した折紙を印刷用のパターンに変換したり、任意の多面体からそれを折るための印刷パターンを計算したりすることも可能になっている。
研究は宮城大学などと共同で、科学技術振興機構(JST)の支援を受けて行い、7月26日に論文誌「ACM・トランザクションズ・オン・グラフィクス」に掲載。8月6日~10日に米ロサンゼルスで開催されたコンピューターグラフィック関連の国際会議で発表した。
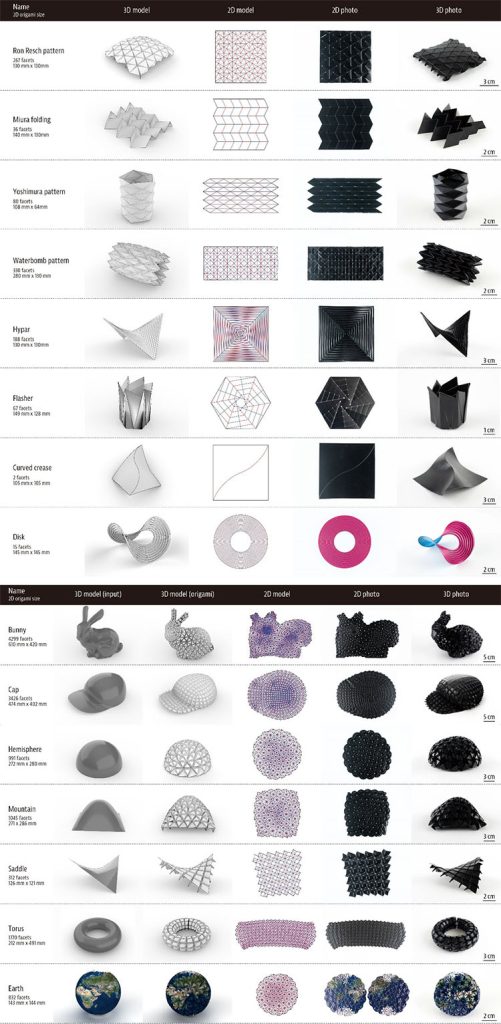
2社と商品化を検討中
研究室で実際につくったばかりの折紙シートを持たせてもらった。見た目とさわり心地は、巻き寿司に使う海苔だった。そして、海苔と同じく加熱で縮む。海苔のようだというとありがたみが少し減ってしまうようだが、鳴海特任講師は「特定の業種や会社名はいえませんがすでに2社と商品化が検討されています」と話し、企業の折り紙シートへの関心は高まっている。
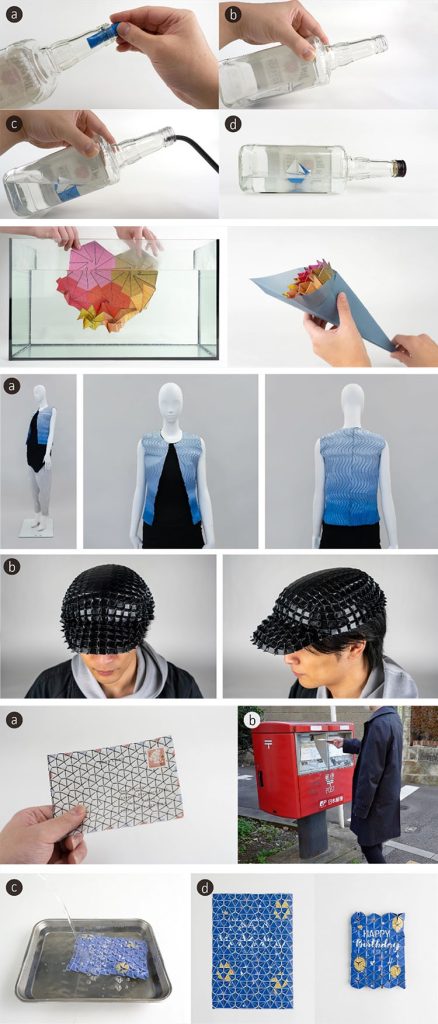
折り紙が自己折りされる技術により、プリーツを多用する服飾といったアパレル業界から、体内で構造物を広げるステントなど医療業界、太陽光パネルや人工衛星の羽など打ち上げ輸送時にコンパクトさが求められる宇宙産業まで大小のものづくりに貢献できる。世界からかっこいいと捉えられる「クールジャパン」として国内外の人々を魅了する可能性が感じられた。
関連リンク
- 東京大学工学部プレスリリース「折紙シートが自動で望みの立体に」
- 研究紹介動画(東京大学川原研究室)
- つながるかたち展2.5 NTT ICCで開催中(帽子の実物を見られる)