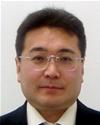
切削工具
私たちの身の回りにある金属部品は、何らかの方法で目的の形状になるように曲げたり、伸ばしたり、削ったりといった加工が施されている。これらの加工法の中で「切削」とは「金属を切り削ること」(広辞苑)であり、このときに用いられる工具が、そのまま「切削工具」である。
切削工具用の硬質材料
金属を削るのであるから、切削工具には金属に対して十分な硬さが必要である。硬さは切削工具の耐摩耗性に置き換えることができ、工具の摩耗しやすさを示す尺度となる。また、被加工物の形状や素材の種類によっては、工具が欠損することもあり、この場合は十分な「靭性(じんせい)」(壊れにくさ)が必要になってくる。 Fig.1では、一般に用いられる切削工具材料を両尺度によって整理した。概して硬さの高い材料ほど靭性は低下する傾向にあり、これは、加工する被加工物や加工条件によって最適な工具材料を使い分けることが必要であることを示す。
![]() |
Fig.1 一般的な切削工具材料の硬さと靭性の関係 |
切削工具の中で、最も多く用いられる硬質材料が「超硬合金」である(最近は、超硬合金単体で工具に用いられることは少なく、耐摩耗性を向上させる目的で、表面にセラミックスを被覆した工具が一般的)。
超硬合金は「WC(タングステンカーバイド)-Co(コバルト)」からなる合金で(Fig.2(a)参照)、そのWCの粒度やCo量を調整することで、硬さや靭性を制御することができるため、幅広い加工条件に対応することができる。例えばFig.2(b)のように、耐熱性や耐反応性を改善する目的で、TiC(チタンカーバイド)、TaC(タンタルカーバイド)を添加する場合もある。
一方「サーメット」は、超硬合金と比較すると、「WC」の替わりにTi(C、N)を、「Co」の替わりにNi(ニッケル)を使用し、さらに靭性改善の目的で他炭化物を添加した合金で(Fig.2(c)参照)、硬質相は、黒色のTi(C、N)のコア部分と、その周辺の灰色の(Ti、W、Ta)(C、N)のリム部分からなるのが一般的である。サーメットの切削特性は超硬合金よりも耐摩耗性に優れるものの、耐欠損性は十分ではなく、使用できる範囲が限定される。
切削工具として有用な超硬合金であるが、その主成分となるWCの原料であるWは希少・偏在金属のため、その安定供給は大きな課題であり、この代替材料の開発、またはW使用量を低減した材料の開発が求められている。
本稿では、サーメットの特性を改良することより超硬合金の使用領域を代替し、工具としてのWCの使用量を削減する事例を紹介する。
![]() | ![]() | ![]() |
(a)一般超硬合金 (WC-Co系) 多種多様な用途 | (b)一般超硬合金 (WC-TiC-TaC-Co系) 耐熱 耐反応性の用途 | (c)サーメット (WC-TiC-TaC-Co系) 耐熱 耐反応性の用途 |
Fig.2 一般的な超硬合金とサーメットの組織例 |
超硬合金が工具として有用な理由
切削時の工具刃先の温度は、被削材や条件にもよるが、900℃を超える場合も少なくない1)。切削時には、室温からこのような温度まで瞬間的に変化し、工具刃先には非常に大きな熱負荷が生じる。このような環境で、超硬合金が幅広く用いられる理由のひとつに、高い「熱衝撃破壊靭性値」がある。
これは、次式で与えられる。
R2C=(λ・KIC)/E・α
R2C:熱衝撃破壊靭性値(W・m-1/2)、λ:熱伝導率(W/m・K)、KIC:破壊靭性値(MPa・m1/2)、E:ヤング率、α:熱膨張係数(x10-6/K)
Table1に、市販の超硬合金とサーメットのそれぞれの値を示す。これより熱衝撃破壊靭性値は超硬合金がサーメットより、はるかに高い値を示すことがわかる。すなわち、サーメットを用いて超硬合金の代替を行うためには、サーメットの熱伝導率と破壊靭性値を向上させることが必須である。
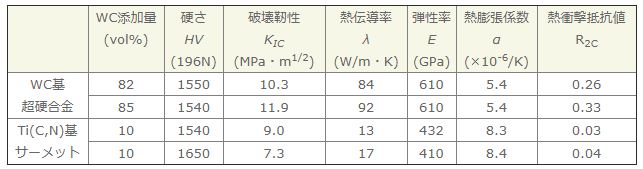
サーメットの熱伝導率と破壊靭性値
サーメットの特性を改善する目的で、硬質相であるTi(C、N)に金属を固溶させた粉末を用いることを試みた。
Fig.3は、固溶金属種(X)が、(Ti0.9X0.1)(C0.5N0.5)固溶体の熱伝導率および「ビッカース硬さ」にどのような影響を及ぼすかを調べた結果である。一般に、金属を固溶させることで、熱を伝える「フォノンの散乱」が増加し、熱伝導率は未固溶の場合よりも低下する。ところが、低下する割合は一様ではなく、Zr(ジルコニウム), Nb(ニオブ)およびTaを固溶させた場合は、ほかの金属を固溶させた場合よりも低下する割合が小さいことがわかる。また、Zr固溶で硬さは低下したが、NbおよびTaを固溶させると硬さは上昇した。つまり、硬質相のTi(C、N)にNbやTaを固溶した固溶体粉末を用いたサーメットとすることで、同一硬さで比較した場合に、熱伝導率の低下を最小限に抑制し、破壊靭性値などの特性が改善できると思われた。
![]() |
Fig.3 熱伝導率および硬さに及ぼす固溶金属種の影響 |
Fig.4では、Ti(C、N)にNb、Moをあらかじめ固溶させた粉末を用いて製作したサーメット(a)と、これと同じ組成となるように各々の粉末を用いて調整したサーメット(b)の破壊靭性値と硬さとの関係を示した(焼結温度を変化させた試料)。ここで、Mo(モリブデン)は金属相との「濡れ性」を改善する目的で同時に固溶させた。図より、いずれの試料も焼結温度が高くなるほど、ビッカース硬さは減少し、逆に破壊靭性値は増加する傾向を示した。また、同一の硬さで比較すると、固溶体粉末(a)を用いたほうが、各々の粉末を用いた場合よりも高くなることも分かる。すなわち、NbやMoを固溶体させた粉末を用いてサーメットを作製すると、破壊靭性値を向上させることが可能である。また、WCは他の炭化物に比べて、熱伝導率が高く、熱膨張係数が小さい。従って、WCをサーメット中に添加、残存させることで、熱衝撃破壊靭性を向上させることができると考えられる。
![]() |
Fig.4 固溶体粉末を用いた場合と、各々の原料粉末から調整した場合の破壊靭性値と硬さとの関係 |
試作サーメットの切削性能
Fig.5には、添加WC量と金属量を種々変化させた固溶体粉末を用いた試作サーメットと、比較のため市販超硬合金、サーメットを用いて、切削性能を比較した結果を示す(右軸にはそれぞれの破壊靭性値も記した)。切削試験条件は、次の通り。被削材:合金鋼SCM440-JIS、切削速度(Vc)=150m/min, 切込み(ap)=2.0mm, 刃辺り送り(fz)=0.3m/tooth, 乾式切削で行い、工具が欠損するまでの距離を評価した。金属量が多くなるほど、破壊靭性値が高くなり、工具が欠損するまでの加工距離は長くなった。特に、WC量を40%、金属量を16%とした試作サーメットは超硬合金以上の耐欠損性を示している。
![]() |
Fig.5 試作サーメットと市販超硬合金、サーメットの耐欠損性の比較 |
同試料を用いて、耐摩耗性を調べた結果をFig.6に示す。試験条件は次の通り。被削材:合金鋼SCM440-JIS、切削速度(Vc)=200m/min, 切込み(ap)=2.0mm, 刃辺り送り(fz)=0.15m/tooth, 乾式で6mを切削し、各工具の平均逃げ面摩耗量を評価した。30%WC/12Me試料の耐摩耗性が最も悪くなっているが、これは金属量が少なすぎ、微小チッピングに因るものである。他の試作サーメットは、市販サーメットには及ばないものの、超硬合金よりも耐摩耗性に優れていることがわかる。両切削試験から、試作サーメットは超硬合金の切削領域の一部を代替できると思われた。
![]() |
Fig.6 試作サーメットと市販超硬合金、サーメットの耐摩耗性の比較 |
まとめ
希少・偏在元素のWを多く使用する超硬合金切削工具の代替として、サーメットの改良を試みた。固溶体の硬質相粉末を使用する、WCを添加するなどの方法で、一部の切削領域では超硬合金と同等の切削性能を確認できた。このような技術を用いることで、切削工具に使用するWの量を削減することができると考えられる。また、同じ目的に対して、サーメットと超硬合金を焼結・接合する試み2)や、サーメットの表面改質によって破壊靭性を改善する試み3)など、様々な提案がなされており、さらに“省W技術”が進歩することが期待される。
〈謝辞〉本研究の一部は、NEDO(新エネルギー・産業技術総合開発機構)の「希少金属代替材料開発プロジェクト」委託事業により実施したもので、ここに謝意を表します。
〈参考文献〉
- 篠塚淳、内海幸治、バスティ・アリ、帯革利行『日本機械学会論文集(C編)』(72巻717号〈2006-5〉1687)
- 石田友幸、森口秀樹、池ヶ谷明彦『粉体粉末冶金協会 平成23年度秋季大会』(194)
- 竹澤大輔、原宏樹、高橋俊行、木下聡、林宏爾『粉体粉末冶金協会 平成22年度秋季大会』(194)
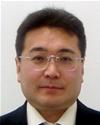
(たかはし としゆき)
高橋 俊行(たかはし としゆき)氏のプロフィール:
1964年岩手県生まれ。県立福岡高校卒業。1987年岩手大学工学部応用化学化卒業、株式会社タンガロイに入社。高硬度材加工用アルミナ基セラミックスの開発、鋳鉄加工用窒化珪素セラミックスの開発などに従事。2011年5月から現職。