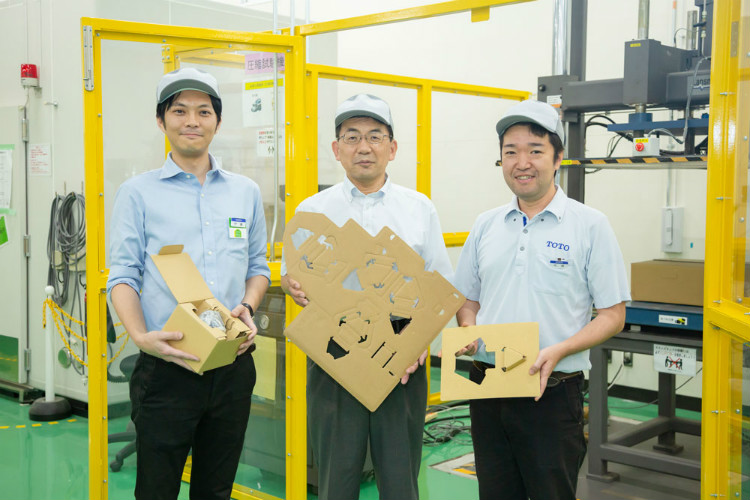
品物を買うとき包装に注目したことがあるだろうか。製品を守るのに不可欠な包装。これに目を向けると、製品を提供する企業の環境への思いが見えてくる。
トイレなどの水まわり製品の製造、販売で知られるTOTO株式会社は、今から20年前に従来の発泡スチロール製の包装材を見直し、リサイクルしやすい段ボール中心の包装に切り替えた。段ボールを材料とした包装材の設計はどのように進められているのだろうか。この分野で貢献している3人に話を聞いた。
製品が消費者に届いたとたんに
包装材は“ごみ”になってしまう
工場で生産された製品が消費者の手元に届けられるまでには、倉庫での保管やトラックなどによる輸送といった流通の過程を経ることになる。輸送中、製品は常に振動による衝撃を受けるし、誤って落とせば、製品に強い衝撃が加わることもある。倉庫で製品が積み重ねられることによって受ける圧力も決して小さなものではないだろう。それでも製品を無事に消費者に届けるため用いられているのが、包装箱の中で製品を保護する役目の「包装材」だ。
特に衝撃に弱い精密機器や陶器製品等を保護するための包装材には、衝撃を和らげる高い性能が求められる。そのため、かつては、発泡スチロールでできた包装材が使われることが多かった。しかし包装材は、製品が消費者のもとに届けられた時点でごみになってしまうものである。このため、近年リサイクルが容易な、より地球環境にやさしい素材が使われるようになってきた。
TOTOは、1999年に温水洗浄便座「ウォシュレット※」の包装材を従来の発泡スチロールから段ボール製に切り替えた。その経緯について、同社ウォシュレット開発第三部包装・印刷物グループ参与の青柳尚樹さんはこう説明してくれた。
※「ウォシュレット」はTOTOの登録商標
「かつては包装材の素材にこだわりはなく、発泡スチロールも使っていました。しかし、より環境に配慮した製品が求められるようになり、それは同時に製品を保護する包装材にも求められるようになったのです。そこで材質を発泡スチロールから段ボール中心に切り替えることにしたのが1999年のことです。環境性能という観点から、卵パックなどに使われるパルプ繊維を成型したパルプモールドの使用も検討しましたが、表面のざらつきが樹脂製のウォシュレットの表面を傷つける恐れがあることから、表面が平滑な段ボールを採用することにしました」
一般的な段ボールは3層構造になっており、ライナーと呼ばれる厚紙2枚(表ライナー、裏ライナー)と、波型に成形した中芯を接着剤で貼り合わせて作られている。このような構造の段ボール自体にも衝撃吸収性があるとはいえ、むき出しのウォシュレットを箱詰めしただけでは、製品が壊れないようにするのは難しい。そこで段ボールでできた包装材に十分な緩衝性能を持たせるために、包装材の形状や構造を検討する必要が出てくる。さらに環境への配慮も必要だ。これらをトータルに考えて実現させるのが「包装設計」だ。TOTOはこの「包装設計」に力を入れている。
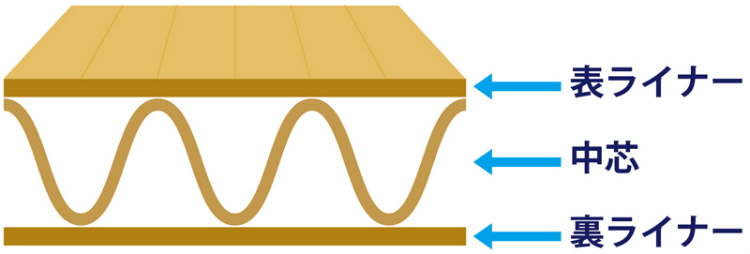
段ボールを折りたたみ様々な形状を作ることで、緩衝性能を高め、製品を保護しようという取り組みだが、段ボールを用いた包装材の設計を進めるには社内の組織改革が必要だったと青柳さんは説明する。
「段ボール中心に切り替える以前、包装材の設計は外部のメーカーに委託していました。ある程度、製品の開発が進んだ時点で製品の仕様を伝え、発泡スチロール製の包装材を作ってもらっていたのです。しかし、流通過程で加わる衝撃に対して、過不足のない緩衝性能を段ボールに持たせるように設計するには、製品の仕様を熟知している製品設計担当者との連携が必要であると考えました。段ボール中心に切り替える時代に組織改革を行い、製品開発の同じ部門で包装設計を行うようになりました」
製品設計との密な連携で
最適な包装設計を実現
そもそも製品は、使用時に求められる強度が備わるように設計されている。例えば、ウォシュレットであれば、人が座って壊れないだけの強度が備わっている。しかし流通過程ではトラックの振動や積み下ろしの際の衝撃など、いわゆる“輸送ストレス”が加わるため、製品の強度に包装材の強度を加える必要がある。
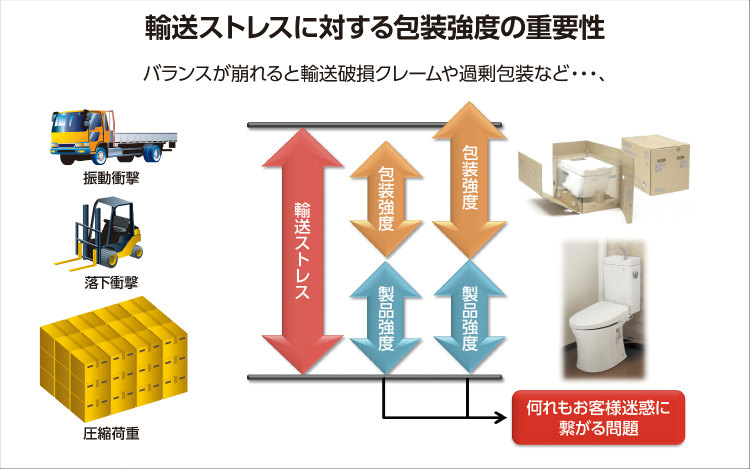
もし製品強度と包装強度を足しても輸送ストレスを下回るようであれば、流通過程で製品が破損するリスクは高まるだろう。かといって、輸送ストレスを大幅に上回る強度の包装材にしては、過剰包装になってコストの増大を招いてしまい、いずれにしても製品購入者に不利益を与えてしまう。青柳さんはこう続ける。
「包装設計の担当者は、輸送ストレスに対して過不足のない包装材を作るため、製品に加わる輸送時の衝撃などはおおむね把握しています。ですから、製品強度に、どの程度の強度を補える包装材であれば輸送ストレスに耐えられるか分かっていますが、包装材だけで強度を補うことが難しい場合は、製品設計の担当者に製品自体の強度を高めてもらうことをお願いしなければなりません。だからこそ、包装設計をする者が製品設計をする者と同じ部門にいることに大きな意味があるのです」
実際の包装設計の手法について、同グループの佐藤賢志さんが説明してくれた。
「包装材を設計するのに専用のソフトウェアがあるわけではありません。一般的な設計用のソフトを使って設計しています。設計後はサンプルカッターと呼ばれる設備で実際に段ボールを切り出し、組み立てた包装材に製品を梱包して、きちんと保護できるかどうか、落下試験や圧縮試験などを行って確認します」
動画:サンプルカッター
動画:落下試験
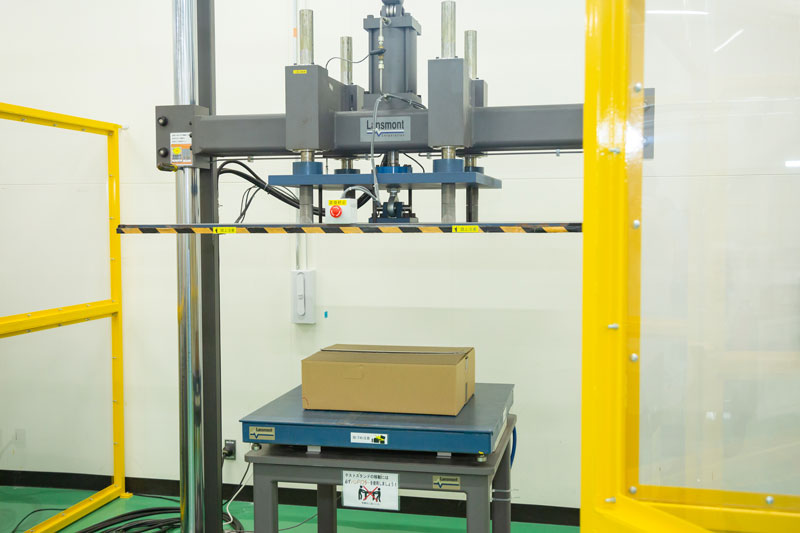
例えば、落下試験を行う際は、製品に加速度センサーを取り付け、落下時の製品にかかる衝撃値を測定。製品が破損するほどの衝撃が加わってしまう場合は、包装設計をやり直して再度包装材の試作品を作り、さらに試験を行って……という試行錯誤が繰り返される。しかも、段ボールの強度などの状態は環境の影響を受けて大きく変化する。気温、湿度が高まれば、空気中の湿気を多く吸い込み、強度は大幅に低下してしまう。従って、正確な試験や評価を行うために、環境を一定にした部屋に24時間段ボールを放置してから実験を行うようにしている。
こうして包装設計に関する経験が蓄積されてきたことにより、徐々に包装材の性能は向上し、20年前に包装材を段ボール中心に切り替えてから現在までの間に、部材費で約70%減、組み立て作業費で約60%減と大幅に削減できているという。同グループの伊藤勇樹さんがこう続ける。
「包装材は、100人が設計すれば、100通りのものができるのではないかと思えるぐらい、設計者のセンスが大きく影響するものです。そのセンスを生かして、これまで様々な新しい包装材が作られてきました。包装設計を行うための特別なツールはありません。設計者の職人技ともいえる独自の発想と工夫の積み重ねこそが一番のツールといえます」
スープが絡む縮れ麺を参考に
部品を保護する包装箱を設計
新しい包装材の一例として挙げられるのが、立体構造緩衝材だ。それまでの包装材は製品を包み込むように保護しており、包装材と製品は“面”で接していた。これを見直し、製品に“点”で接する包装材に変更。段ボールを組み立てて立体構造の緩衝材を作り、点で接して製品を保持することで、十分な緩衝性能を持ちつつ、消費する段ボールを減らすことができた。青柳さんがこう続ける。
「この立体構造緩衝材で重要なことは、誰もが簡単に組み立てられるということです。一枚の段ボールから一つの立体構造を作り出すのにかかる時間はほんの数秒ですから、組み立てコストの軽減にも貢献できます」
動画:立体構造緩衝材
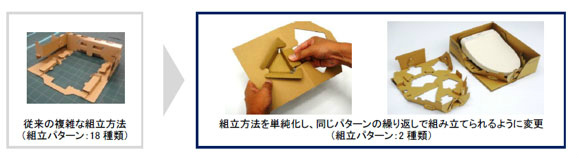
この立体構造緩衝材をはじめとして、ほとんどの包装材は製品ごとに設計される。だが、故障した製品を修理する際に必要な補修部品等は形状がばらばらなので、部品それぞれ個別に包装材を作ることは難しい。そのため形状が異なる部品に対応できる包装材が求められ、形の異なる内容物にフィットする緩衝機能付き包装箱が開発されたのだ。
この包装箱は一部に波型の切れ込みが入れられているので、ここに部品を押し込むと、部品を網が包み込むように受け止め、箱の中で浮かせて輸送時の衝撃から部品を守るようになっている。この包装箱の開発に関わった伊藤さんはこう語る。
「箱に切れ込みを入れて、そこに部品を押し込むことにしたのですが、押し込んだ後にしっかり部品を保持できる切れ込みの形状がなかなか見出せませんでした。そんな時、ふとラーメンは縮れ麺の方が、スープがよく絡むという話を耳にして、部品と絡んでしっかり保持できるかもしれないと考えました」
そして採用されたのが縮れ麺を模した波型の切れ込みだった。これに部品を押し込むと、伊藤さんが期待した通りに、部品をしっかり保持できるようになった。「包装設計は設計者のセンス次第」というのが納得できる。
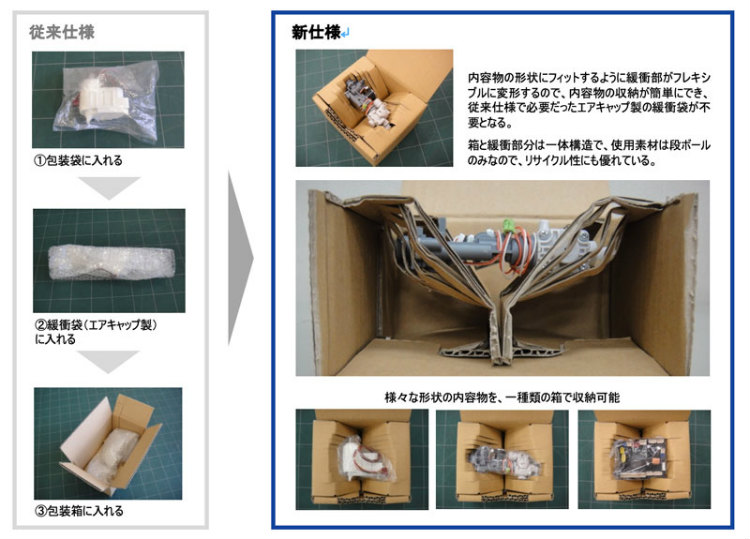
今後、設計者のセンスを生かして、どのような包装設計に取り組もうとしているのかと問うと、青柳さん、伊藤さん、佐藤さんは、三人三様の将来展望を語ってくれた。
「包装設計を進めた結果、段ボールの量、組み立ての手間ともに軽減したとはいえ、技術開発によってまだまだ減らせるでしょう。その結果、包装材の製造、輸送によるCO2の排出を抑え、包装廃棄物を減らしてSDGsの実現に貢献していきたい」(青柳さん)
「人手不足に加えて、働き方改革が求められています。組み立てやすい包装材の開発が求められているわけですが、そのようなニーズに応えるためにも、組み立ての自動技術の開発を進めてもいいのではないでしょうか」(伊藤さん)
「人材の多様性(ダイバーシティ)を考えると、体の不自由な方々にも組み立てられる包装材にしていかないといけないと思います。これまで両手でなければ組み立てられなかったものが、片手で組み立てられるようになれば、より多様な人に組み立て作業に従事してもらえますから」(佐藤さん)
それぞれの将来展望の視点は異なるが、見据える先は同じ「豊かな未来社会」。これからも職人技ともいえる包装設計は脈々と受け継がれ、環境に最大限の配慮をしつつ、TOTOの製品を優しくしっかりと包み込んでいくのだろう。
コラム1 段ボールのバネ性を利用した“潰れない”緩衝仕切
ウォシュレット製品と包装箱の間に設置するために開発された「段ボールのバネ性を利用した“潰れない”緩衝仕切」。段ボールを折ることで実現するバネのような反発(バネ性)を利用して、様々な衝撃を吸収する構造になっている。段ボールの一度潰れてしまうと緩衝機能を失うという弱点を克服した画期的なアイデアとして、2018年度の「ジャパンスター賞」「アジアスター賞」「ワールドスター賞」に加え、「第43回木下賞 包装技術賞」を受賞した。
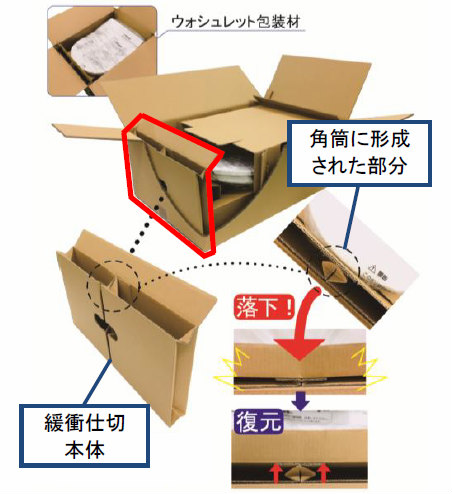
コラム2 TOTOのSDGsへの取り組み
TOTO株式会社では、2018年4月から、これまで取り組んできた“環境”というテーマに、事業に関係の深い “きれいと快適”“人とのつながり”を加えた新たな「TOTOグローバル環境ビジョン」をスタート。この3つのテーマを中心に、様々な活動を通じてSDGsにも貢献している。
TOTOが掲げるミッションのマテリアリティの1つとして環境問題へ取り組んでおり、国内で再利用の仕組みが整っている段ボールにこだわりを持って包装材に使用しているのも、その取り組みの一つです。
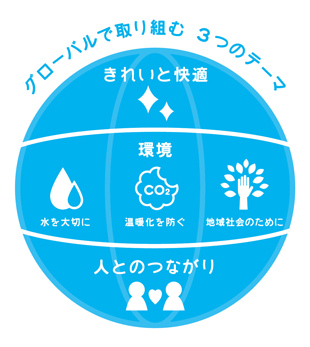
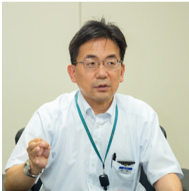
ウォシュレット開発第三部
包装・印刷物グループ
参与
青柳尚樹さん
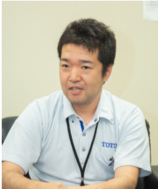
ウォシュレット開発第三部
包装・印刷物グループ
佐藤賢志さん
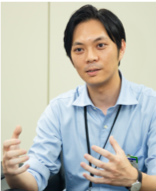
ウォシュレット開発第三部
包装・印刷物グループ
伊藤勇樹さん